One-step intelligent rubber refining production line of Yiyang Rubber & Plastics Machinery officially put into operation
Updated:2018-07-17 11:22:12
Views:
After nearly one year's installation and trial run, the one-step intelligent rubber production line developed by Yiyang Rubber Machinery was successfully accepted and handed over by Guiyang Hongyang Sealing Parts Co., Ltd. and officially put into operation.
Less operator and higher productivity on this automated production line. The operator can monitor the operation of the production line through the display screen. The weighed raw materials are transported by belt to the tandem mixer for rubber mixing. After the refining in the lower mixer, it is automatically sent to the intelligent mixing unit to repeatedly press the rubber and then sent into the automatic filter machine to filter the impurities. After film cooling, the film is automatically and continuously produced. And the whole process is highly automated.
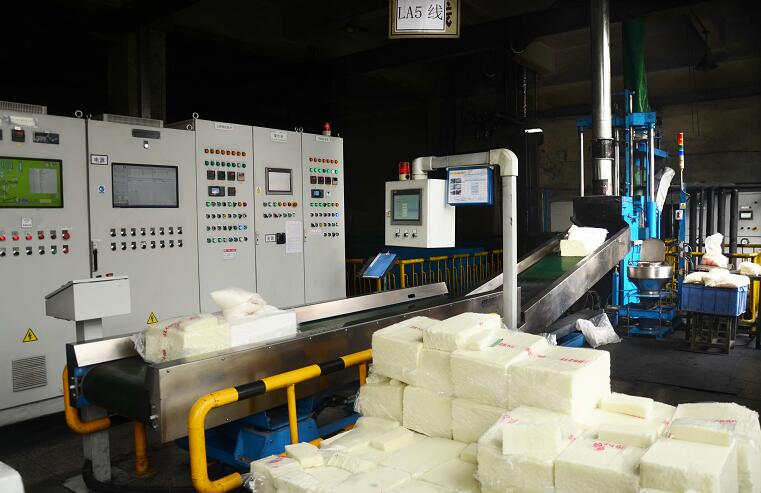
According to reports, compared with the traditional rubber refining method, the production capacity can be doubled by using a tandem mixer to complete the final refining and masterbatch process in one time. Both the masterbatch and the final refining are controlled by the rubber processing management system. The quality is uniform and stable, the filling powder and the small material assistant are all closed transport and closed mixing, which produces less pollution.
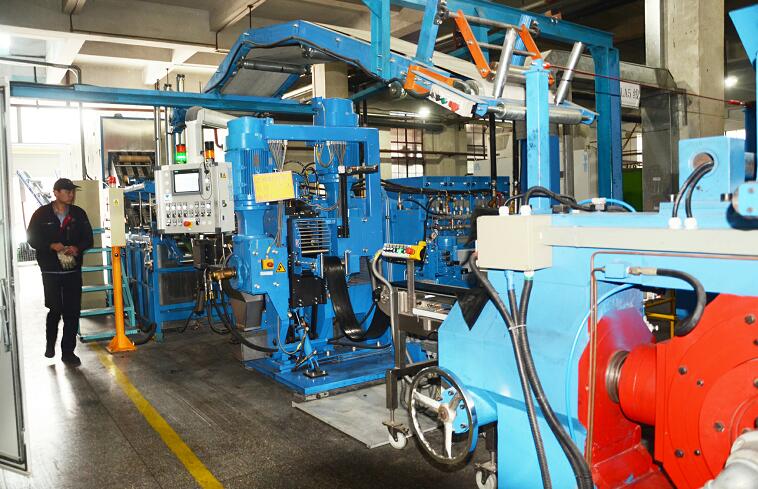
Among them, the new type of wear-resistant ring seal device adopts c-c composite material and does not need to add any oil, which not only avoid the oil contamination of the rubber and the environment, but also the tandem mixer can save about 40% of the oil every day. At the same time, using tandem mixers, the rubber production line not only takes up less space, saves civil construction investment, but also reduces the staffing by half. The on-line automatic rubber filter can greatly improve the quality of the filter grubber, which has a small temperature rise and a small change in the viscosity of the rubber before and after the filter. No fumes are generated during the production process, and a clean working environment for the filtration site can be maintained. In the process of film cooling and producing, the film is automatically divided into three equal parts and three lines through the filter machine for repeated cooling and the final film is perfectly matched to the size requirements of the seal vulcanization.